Top Heat Exchanger Maintenance Tips to Extend Equipment Life
- Teknoflow SEO
- 4 days ago
- 2 min read
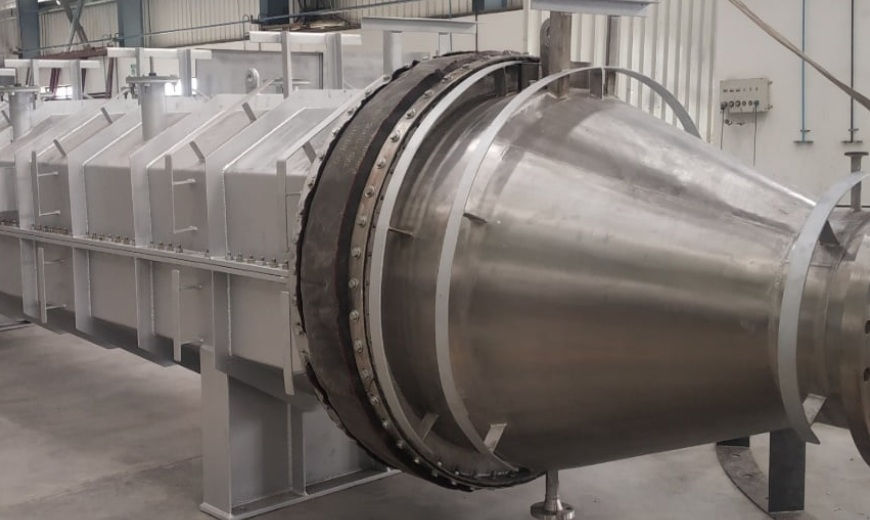
Regular maintenance of heat exchangers is essential for keeping industrial thermal systems running efficiently. These units are responsible for transferring heat between fluids, a process critical to many operations. Over time, dirt, scale, and corrosion can build up inside the exchanger, reducing heat transfer efficiency. This results in higher energy consumption and puts extra strain on the system. If ignored, poor maintenance can lead to equipment failure, unplanned downtime, and costly repairs. Keeping
heat exchangers clean and in good condition ensures optimal performance. It also extends their lifespan and improves overall system reliability.
Top Heat Exchanger Maintenance Tips
1. Conduct Routine Inspections
Regular visual and thermal inspections can detect scaling, corrosion, or leaks early. Early detection prevents costly breakdowns.
Tip: Use infrared thermography and ultrasound tools to assess performance.
2. Clean Heat Exchanger Surfaces
Deposits like scale, sludge, or biofilms reduce thermal efficiency.
Tip: Use chemical cleaning agents or CIP (Clean-in-Place) systems approved by the heat exchanger manufacturer in India.
3. Monitor Temperature Differentials
A sudden drop in temperature differential can signal fouling or flow blockages.
Tip: Keep logs of inlet and outlet temperatures for early diagnostics.
4. Replace Worn Gaskets and Seals
In plate heat exchangers, gaskets wear out over time, causing internal leaks.
Tip: Use OEM parts from trusted heat exchanger suppliers in India.
5. Follow Manufacturer’s Maintenance Schedule
Each heat exchanger model has unique maintenance needs. Skipping regular service can lead to early failure or warranty issues.
Tip: Stick to the recommended schedule for inspections, part replacements, and cleaning procedures of the heat exchanger manufacturer
6. Check for Pressure Drops
A noticeable pressure drop across the heat exchanger often means there’s a blockage inside. This can reduce system flow and efficiency.
Tip: Track pressure readings during operation. If you see a consistent drop, it’s time to clean or inspect the unit.
Final Thoughts
For any industrial setup using a heat exchanger in India, preventive maintenance ensures longer equipment life, higher energy efficiency, and lower operating costs. Whether you use plate heat exchangers or shell-and-tube systems, proper upkeep saves money and downtime. In the Indian context, where climate, water quality, and operating conditions vary widely, adopting a site-specific maintenance plan becomes even more crucial. Using certified technicians, proper water treatment, and timely part replacement will further extend the equipment's lifespan and help maintain compliance with safety standards.
FAQS
Q1. How often should a heat exchanger be cleaned?
Ans: Cleaning intervals vary by industry and usage, but every 6–12 months is a good standard.
Q2. What’s the difference between plate and shell heat exchangers?
Ans: Plate heat exchangers are compact and easy to clean, while shell-and-tube types handle higher pressures and temperatures.
Q3. What are common signs that a heat exchanger needs maintenance?
Ans: Common warning signs include a drop in heat transfer performance, increased energy use, unusual pressure drops, fluid leaks, and visible corrosion. Regular inspections can help catch these early.
Comentários